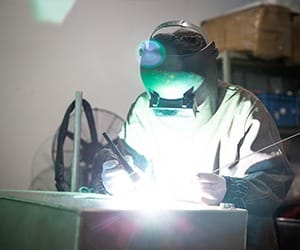
CNC machining stands as/among/at the pinnacle of precision engineering, utilizing advanced computer-aided manufacturing (CAM) to create complex and highly accurate parts.
A robust/versatile/sophisticated machine tool controlled by a programmable computer/system/controller, CNC machining processes materials like metal, plastic, and wood with exceptional accuracy/detail/precision. This technology is widely/extensively/commonly employed across diverse industries, from aerospace and automotive to medical devices and electronics.
CNC machining offers numerous advantages, including:
* High/Exceptional/Unrivaled accuracy and repeatability
* The ability to create intricate designs with complex geometries
* Efficient/Rapid/Fast production times
* Minimized material waste/loss/consumption
This makes CNC machining an indispensable tool for engineers and manufacturers seeking/demanding/requiring the highest level of precision and quality in their products.
Understanding CNC Machining Processes

CNC machining processes are seem complex at first glance, but they're fundamentally about precisely controlling tools to form materials.
A computer program controls the machine, executing instructions with extraordinary accuracy. This allows machinists to produce intricate parts in a wide range of applications, from automotive components to household goods.

Let's break the basic principles behind CNC machining:
*
Software tools are used to create digital blueprints of the desired parts.
* These blueprints are then converted into machine-readable code, known as G-code.
* The G-code guides the CNC machine on where to move and what operations to carry out.
By means of this automated process, CNC machining offers superior precision, repeatability, and output.
Unlocking Design Potential with CNC Milling
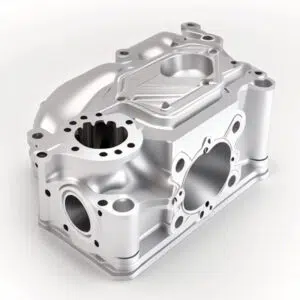
CNC milling has become an indispensable tool transforming the world of design and manufacturing. With its exceptional precision and versatility, it empowers designers to bring their most ambitious ideas to life, crafting complex geometries and intricate details that were once unimaginable. From prototypes to production runs, CNC milling offers a robust platform for realizing diverse designs across various industries.
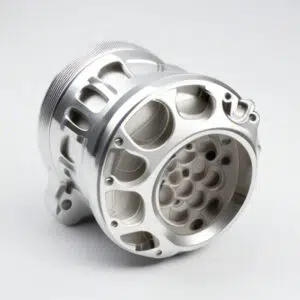
One of the key strengths of CNC milling lies in its ability to work with a wide range of materials. Whether it's hardwoods, softwoods, metals, plastics, or composites, CNC machines can efficiently mill and shape these substances with accuracy and consistency. This flexibility allows designers to experiment with different materials and textures, creating unique and eye-catching designs.
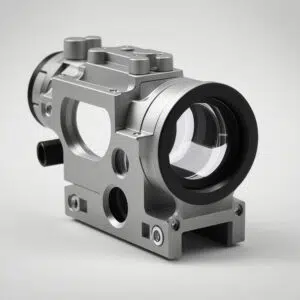
Moreover, CNC milling enables rapid prototyping, significantly minimizing the time it takes to bring a design from concept to reality. Designers can quickly create functional prototypes for testing and refinement, iterating on their ideas with ease. This iterative process fosters innovation and expedites the overall design cycle.
Turning Complex Geometry into Reality with CNC Turning
CNC turning has revolutionized the way we manufacture intricate components. By leveraging sophisticated computer-aided design programs, even the most complex geometrical shapes can be translated into tangible objects. This process involves precisely controlled cutting tools that revolve against a stationary workpiece, gradually shaping it to the desired form. The resulting accuracy is unparalleled, enabling manufacturers to create components with tight tolerances and complex features that would be impossible to achieve using traditional methods.
This technology has gained widespread application in a variety of industries, from aerospace and automotive to medical devices and consumer electronics. CNC turning empowers engineers and designers to push the boundaries of what's possible, bringing their imaginative concepts to life with exceptional fidelity.
Tapping into The Power of Automation: Exploring CNC Operations
Computer Numerical Control (CNC) operations have revolutionized the manufacturing/production/fabrication industry by automating intricate and repetitive tasks. CNC machines, guided/controlled/programmed by sophisticated software, execute precise movements with incredible accuracy and repeatability. This empowers/enables/facilitates manufacturers to produce high-quality components at an unprecedented speed/rate/volume. From machining metals and plastics to carving wood and foam, CNC operations have become indispensable in a wide range/spectrum/variety of applications, boosting/enhancing/accelerating productivity and lowering/reducing/minimizing production costs.
- Furthermore/Moreover/Additionally, CNC machining offers unparalleled flexibility.
- Programmable/Configurable/Customizable toolpaths allow for the creation of complex geometries and designs that would be challenging/difficult/impossible to achieve manually.
Ultimately/Consequently/Therefore, the power of automation through CNC operations has transformed the landscape/domain/realm of manufacturing, paving the way for greater precision, efficiency, and innovation.
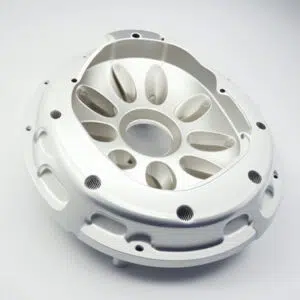
Computer Numerical Control Machining for Prototyping and Small-Batch Production
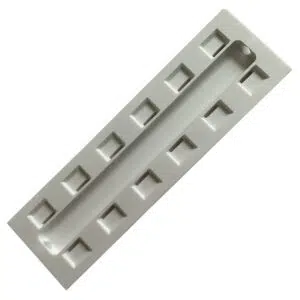
CNC machining has become a vital tool for prototyping and small-batch production in various industries. This versatile process utilizes computer-controlled tools to precisely shape metals, allowing for the creation of intricate parts with high accuracy and repeatability.
The advantages of CNC machining for prototyping include rapid turnaround times, cost-effectiveness for small runs, and the ability to produce prototypes that closely resemble the final product. In small-batch production, CNC machining offers high precision, consistent quality, and the flexibility to manufacture a selection of parts with minimal setup time.
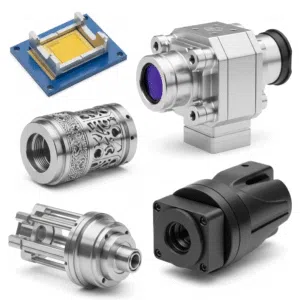
- Furthermore, CNC machining can handle a wide range of materials and complexities, making it suitable for diverse applications.
- Consequently, the combination of accuracy, speed, and versatility makes CNC machining an ideal choice for prototyping and small-batch production.
Achieving Tight Tolerances with CNC Grinding
CNC grinding offers exceptional accuracy for achieving demanding tolerances in various manufacturing processes. By leveraging sophisticated controls and high-speed spindle rotation, CNC grinders can achieve surface finishes within nanometer ranges. Precise workpiece positioning and automated toolpath generation ensure consistency across multiple production runs. Skilled operators can fine-tune grinding parameters such as feed rate, depth of cut, and abrasive selection to optimize performance and meet specific tolerance requirements. CNC grinding is widely utilized in industries ranging from aerospace and automotive to medical device manufacturing, where tight tolerances are critical for functionality and safety.
CNC Fabrication: A Gateway to Customized Manufacturing

In the rapidly evolving landscape of manufacturing, CNC fabrication has emerged as a cutting-edge technology, empowering businesses to create highly customized goods. CNC (Computer Numerical Control) machines utilize precise computer programs to automate the fabrication process, enabling intricate shapes and complex geometries to be brought to life with exceptional accuracy. This level of customization opens up a world of possibilities for industries ranging from aerospace to automotive, allowing manufacturers to cater to specific customer requirements and produce high-quality goods that meet exacting standards.
- Furthermore, CNC fabrication offers several advantages over traditional manufacturing methods.
- {For instance|:, increased production speed, reduced waste, and improved precision.
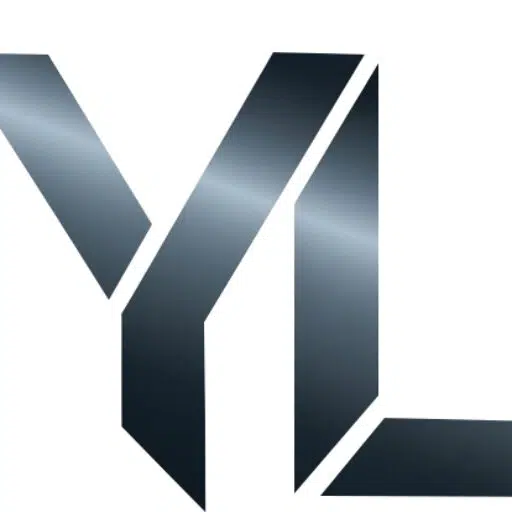
Bridging the Gap Between Material Science and Precision Engineering: CNC Machining Capabilities

CNC machining has emerged as a cornerstone of modern manufacturing, driving the boundaries of precision engineering. This transformative technology seamlessly combines the principles of material science with cutting-edge fabrication techniques. By harnessing the power of Computer Numerical Control (CNC), engineers can fabricate intricate components from a wide range of materials, producing parts with unparalleled accuracy and complexity.
- From aerospace to medical devices, CNC machining plays a vital role in manufacturing high-performance products that meet the most stringent requirements.
- Sophisticated materials such as titanium alloys, ceramics, and composites benefit significant advantages from CNC machining's precision capabilities.
- Additionally, the ability to customize designs at a granular level allows for the creation of bespoke components that maximize functionality and performance.
As material science continues to evolve, CNC machining will remain at the forefront of innovation, driving the development of groundbreaking technologies that shape our future.
Optimizing Productivity Through CNC Programming
In the realm of manufacturing, where precision and efficiency are paramount, CNC programming plays a crucial role. By leveraging the power of Computer Numerical Control (CNC) machines, manufacturers can attain unprecedented levels of accuracy and productivity. A well-crafted CNC program enables the machine to execute intricate designs with remarkable speed. Through meticulous programming techniques, machinists can fine-tune every aspect of the manufacturing process, resulting in significant time and cost savings.
- ,Additionally,, CNC programming reduces the risk of human error, ensuring consistent quality and repeatability in every production run.
- Computerization through CNC programming also frees up skilled machinists to concentrate on more complex tasks, consequently elevating the overall efficiency of the manufacturing operation.
The Future of Manufacturing: Advancements in CNC Technology
The manufacturing landscape is dynamically shifting with the integration of cutting-edge technologies. Among these advancements, Computer Numerical Control (CNC) technology stands out as a transformative tool, propelling increased efficiency, precision, and customization in production processes. From conventional machining to complex 3D printing, CNC machines are setting new standards of what's possible in manufacturing.
One of the most notable innovations in CNC technology is the rise of CNC machining collaborative robots, or cobots, designed to work alongside human operators. Cobots bring a new level of safety and flexibility to the manufacturing floor, optimizing productivity while lowering the risk of workplace injuries.
Moreover, advancements in software and AI are facilitating CNC machines to perform even more complex tasks. Intelligent algorithms can now analyze real-time data to fine-tune machining parameters, resulting in superior products and reduced waste.
The future of manufacturing is undoubtedly intertwined with the continued evolution of CNC technology. As these advancements progress, we can expect even more innovative applications that will transform the industry, leading to enhanced capabilities and a new era of manufacturing excellence.